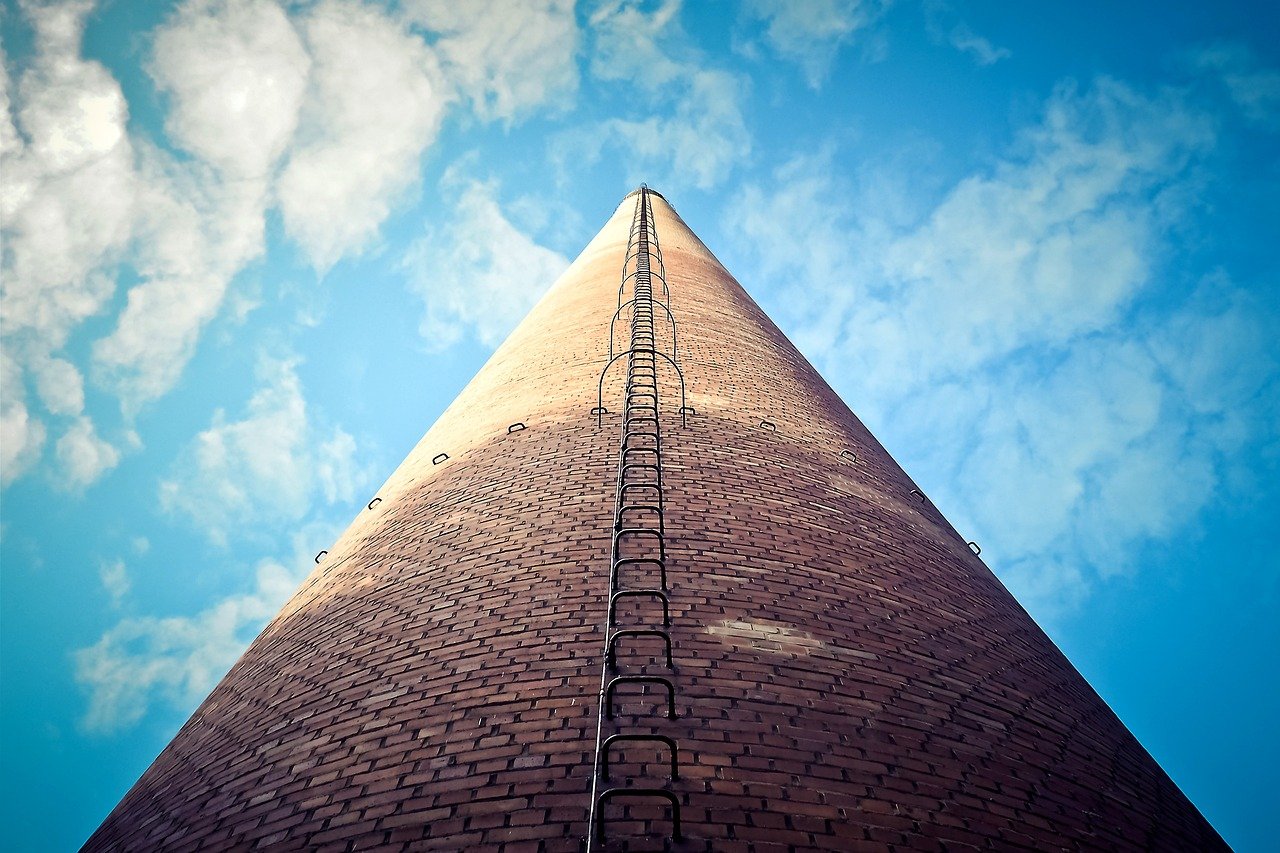
CO2 Derived Products
Task 15 Team
-
Prof. Peter Styring
University of Sheffield
-
Prof. Enrico Andreoli
Swansea University
-
Dr George Dowson
University of Sheffield
-
Dr Craig Armstrong
Swansea University
Synthetic Fuels from Waste CO2 from Steelmaking Processes
Task 15 will take a whole system approach to decarbonising steelmaking processes. It will reduce CO2 emissions through capture and then reuse the CO2 in the production of synthetic fuels. These SynFuels can be used in power equipment or ground transportation on site or used to power maritime and aviation transport. The former is important for steel distribution while the latter helps decarbonise steel transport within the wider supply chain and adds revenue to the mitigation process while providing social benefit [1] in job creation and improved air quality.
The Carbon Dioxide capture system (FluRefin) developed during Task 1 will be made available at steelmaking emitter sites. It is anticipated that the programme will roll out across sites and conclude by the end of 2024. Concurrently, we will work closely with a manufacturing partner to create an OEM FluRefin system through licensing of the Sheffield IP generated under Task 1.
While CO2 can be captured, it is unlikely that there will be infrastructure in place to geologically sequester it for many years and so in Task 15 work will move to the in-situ production of synthetic fuels (SynFuels) from CO2. Research in Task 15 will produce transport drop-in fuels which can be used directly to fuel many applications on-site, including ground transportation (trucks and trains) and heavy machinery, as well as diesel generators. While these are carbon fuels, they are non-fossil fuels as the carbon is recycled. To quantify the environmental impact, data will be provided from the capture studies to Tasks 16 & 18 to carry out LCA studies.
To achieve this, Task 15 will enhance our circular economic approach by re-purposing existing reactor technology. This approach will enable us to use a ‘discovery to production’ approach where catalysts and conditions can be studied at a small scale before being scaled to a larger system on site, interfaced with the FluRefin capture system. It is believed this will be the first time that CO2 from a real emission source will be captured and directly converted to a fuel in the UK. Because of the flexibility of the FluRefin system the process can be tested on any point source emitter on site. This approach will see a significant cost reduction in the production of SynFuels due to the intensified nature of the process integration. SynFuels will be tested to determine the octane/cetane number of the fuels and their suitability as synthetic transport fuels (STFs).
Decarbonisation will require considerable financing if the CO2 is to be treated as a waste. Conversion of the CO2 into SynFuels will provide a revenue stream that can help to finance decarbonisation while avoiding new fossil carbon entering the supply chain. In reality, P2X technologies with carbon avoidance are some of the very few technologies that can be employed in the Net Zero ambition.
Progress to Date
The Synfuels research in Task 15 has focused on both catalyst development and reactor design. A new iron-based heterogeneous catalyst has been developed for the conversion of CO2 directly to ethanol. Small scale reactions have yielded up to 70% conversion and the structure confirmed by 1H NMR. In parallel, a new catalyst system is being developed for the synthesis of middle distillate hydrocarbons. The symbiosis of the approach is exemplified through collaboration across the Flue2Chem project: all the fractions become part of individual supply chains with both surfactant precursors and synthetic fuel fractions being produced concurrently. While these reactions have been carried out using simulated flue gas, we are now moving on to use CO2 captured directly from emitter sites in the next phase. The FluRefin capture unit will soon move to the British Steel site and the captured, refined CO2 used directly in the catalytic reactions. Initial analysis of the captured CO2 shows it to be anhydrous and free from other impurities.
Steelmaking Gases to Value-Added Sustainable Chemicals (SteelGasChem)
Steelmaking gases are a source of carbon dioxide to manufacture chemicals. The future supply chain of fossil-free chemicals is productively linked to unavoidable carbon emissions from the foundation industries. This is true not only at present with carbon intensive BF-BOF route emitting ca. 1.9 tCO2/t crude steel, but also in view of future further deployment of lower carbon footprint EAF releasing ca. 0.1 tCO2/t steel (0.3 tCO2/t steel when adding electricity CO2 intensity) [2]. Globally, defossilisation of the chemical industry can cut over 800 Mt of CO2 per year [3] and steelmaking can play a key role in providing the required carbon dioxide raw material.
The aim of SteelGasChem is to deliver the robust industry-informed production of sustainable and commercially viable chemicals from steelmaking carbon dioxide process and emission gas mixtures.
Task 15 will achieve its aims by delivering the following activities:
Link key industry and academic partners to establish a value chain for the electrochemical conversion of steelmaking CO2 to sustainable commercially valuable chemicals, from raw materials to final products.
Design, build and operate industry-relevant innovative CO2 electrolysers integrating technology from one of the largest and most robust electrochemical industrial processes, the Chloralkali process.
Employ simulated and on-site sampled steel manufacturing gases to perform electrochemical CO2 conversion using the newly developed state-of-the-art electrolysers.
Investigate and implement solutions to improve the resilience of the state-of-the-art industry-informed CO2 electrolysers towards degradation by reactive impurities.
Identify and demonstrate interventions to operate robust CO2 electrolysis using steelmaking gases and safely handle resulting chemical products.
Perform techno-economic analyses to establish CAPEX and OPEX of CO2-to-olefin electrolysis process scale up to establish competitiveness and viability for investment.
To deliver these activities, we will work with our core SUSTAIN industrial partners, The Steel and Metals Institute (SaMI) at Swansea University and Oil & gas / chemical industry consultancy.
Progress to Date
Progress has been made with our iterative designs of falling film electrolysis components for converting carbon dioxide into valuable products. A significant milestone was achieving stable 6-hour operation of a standard gas diffusion electrode through precise monitoring and control of pressure differentials, essential for implementing the falling film approach in CO2 electrolysis. The redesign of our 30 cm tall electrolysis cell represents a notable advancement in improving falling film operation, aiming to enhance efficiency and scalability. The first batch of copper electrodepositions onto the gas diffusion electrodes has been completed, marking an important step in integrating catalysts into the electrolyser. Our team has designed and built a dedicated falling film compartment, enabling us to start comprehensive fluid flow tests and address critical knowledge gaps in falling film electrolyser operation. Progress with SaMI for electrolysis with contaminated gases has facilitated the identification of arrangements and equipment needed to test CO2 gas mixtures relevant to steelmaking.
References:
[1] Styring P; Duckworth EL; Platt EG (2021). Synthetic Fuels in a Transport Transition: Fuels to Prevent a Transport Underclass, Frontiers in Energy Research: Sustainable Energy Systems and Policies, 9:707867. DOI: 10.3389/fenrg.2021.707867
[2] Echterhof, T. Review on the Use of Alternative Carbon Sources in EAF Steelmaking. Metals 2021, 11, 222. https://doi.org/10.3390/met11020222
[3] Centi, G. and Perathoner, S. Status and gaps toward fossil-free sustainable chemical production. Green Chem., 2022,24, 7305-7331. https://doi.org/10.1039/D2GC01572B