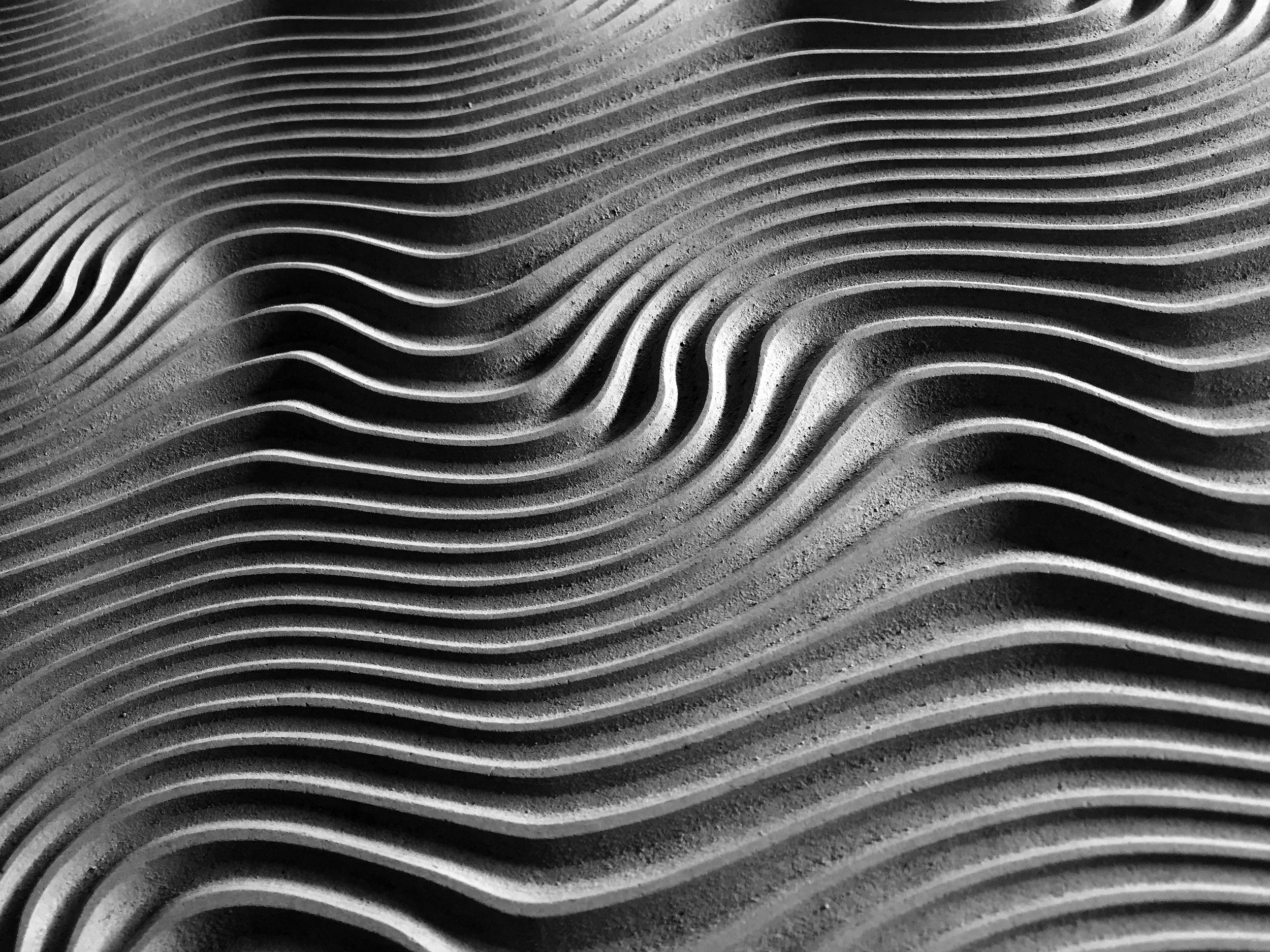
Disruptive Processes
Task 7 Team
-
Prof. Claire Davis
University of Warwick
-
Prof. Zushu Li
University of Warwick
-
Dr Carl Slater
University of Warwick
-
Ajitesh Sharma
University of Warwick
-
Wadah Elagbash
University of Warwick
Introduction
The ever-increasing demand for reducing energy consumption in steel making means that using near-net shape casting is desirable. Different casting options are available, such as belt casting, thick/thin slab casting and strip casting, with associated differences in cooling rate and as-cast thickness. The cooling rates typically range from 0.6 °C/s for conventional thick slab continuous casting, to 500 °C/s for twin roll strip casting with as-cast thicknesses from around 1 mm to 250 mm [1].
It is important to assess how the different casting technologies affect the key metallurgical features that affect subsequent microstructure, and property, development. In addition, the move to greater use of recycled scrap steel means that higher residual element contents will become common in steels and their influence needs to be considered.
This project aims to assess how segregation and as-cast microstructure (e.g., secondary dendrite arm spacing, SDAS) is impacted by moving to these low energy casting technologies, with a particular focus on residual elements. The initial stages of the work have focused on characterisation of as-cast DP800 and S275 steel to understand the effect of cooling rate on the SDAS and segregation behaviour of Mn, as the main alloying element present.
Approach, tests, results and discussion
A DP800 ingot was cast into a 30mm wide mould. The through thickness SDAS was measured. Using the known relationship between cooling rate and SDAS for this material (SDAS = 84CR-0.45 [2]) then a COMSOL model was created, with the boundary conditions defined by fitting with the experimental results.
Using these boundary conditions, a wedge mould, Figure 1 was designed to provide a much greater range of cooling rates that are appropriate for a range of casting techniques from thick slab to thick belt casting (0.455 to 2.895 °C/s for regions of columnar solidification). A wedge mould cast of S275 was and the measured SDAS for both DP800 and S275 can be seen in Figure 2.
Figure 1. The as-cast ingot from the wedge mould
Figure 2: Shows the measured SDAS (μm) against predicted cooling rate (°C/s) ‣ (DP800 and S275)
It was found that S275 and DP800 both show a strong relationship between cooling rate and the resultant SDAS for the cooling rates studied, however they differ, with S275 maintaining a coarser SDAS at the higher cooling rates giving the relationship of SDAS = 97.9CR-0.345 which is likely to be due to the difference in Mn levels between the two steels.
A grid of 350 x 2 EDX points were measured every 1 mm from the cast surface along with the measured SDAS for the same region. The segregation ratio was defined as the local 95% percental value / average Mn content. Figure 3 shows the relationship between the Segregation Ratio (SR) with predicted cooling rate. At slow cooling rates the segregation ratio for both steels is very similar. However, at higher cooling rates the SR for the two steels diverges.
For DP800 a significant reduction in the SR can be seen at higher cooling rates, however for S275 a similar SR ratio is seen over the cooling rate range measured. This can be rationalised using Figure 4 where, at the finer SDAS there is a much greater SR for S275 than the DP steel. Whilst at low cooling rates these materials have similar SDAS (Fig 2), therefore both the time and distance for back diffusion of Mn are similar, at higher cooling rates the DP800 steel has a finer SDAS than the S275 steel, reducing the diffusion distance and allowing for a greater amount of back diffusion. The result indicate that for S275 a faster cooling rate is required to achieve a finer SDAS and but the reduction in time for back diffusion to occur means that a similar SR is maintained.
It is assumed that equilibrium partitioning of Mn occurs during solidification and then the SR in the final as-cast material is affected by the amount of back diffusion. Figure 5 illustrates the two competing factors affecting the SR; 1. diffusion distance
Figure 3: Segregation ratio against predicted cooling rate (°C/s) ‣ (DP800 and S275)
Figure 4: Segregation ratio against measured SDAS (μm) ‣ (DP800 and S275)
Next Steps
The effect of cooling rate on the solidification structure (SDAS) and segregation behaviour when residual elements (particularly Cu, Sn and Ni) are present will be investigated in the next stage of the work. A DP800 composition with the addition of Cu composition of 0.6 wt % will be cast into the wedge mould. Table 1 gives the partition coefficients, obtained from Thermocalc, and diffusion rates of the main elements present at 1480 ℃. The data suggest similar partitioning behaviour but different back diffusion rates for Mn and Cu. The influence of the residuals on the SDAS and then the SR for both Mn and Cu at different cooling rates will be explored.
Table 1. Calculated partition coefficients from thermocalc and diffusion rates of residuals
Figure 5. Balance between diffusion distance (SDAS) and diffusion time (cooling rate) as two competing factors affecting the SR
References
[1] Guthrie, R. I. L. and M. M. Isac "Conventional and near net shape casting options for steel sheet." Ironmaking &
Steelmaking 2016 Vol. 43 Issue 9 Pages 650-658
[2] O. Volkova, H.-P. Heller and D. Janke. ISIJ International 2003 Vol. 43 Issue 11 Pages 1724-1732