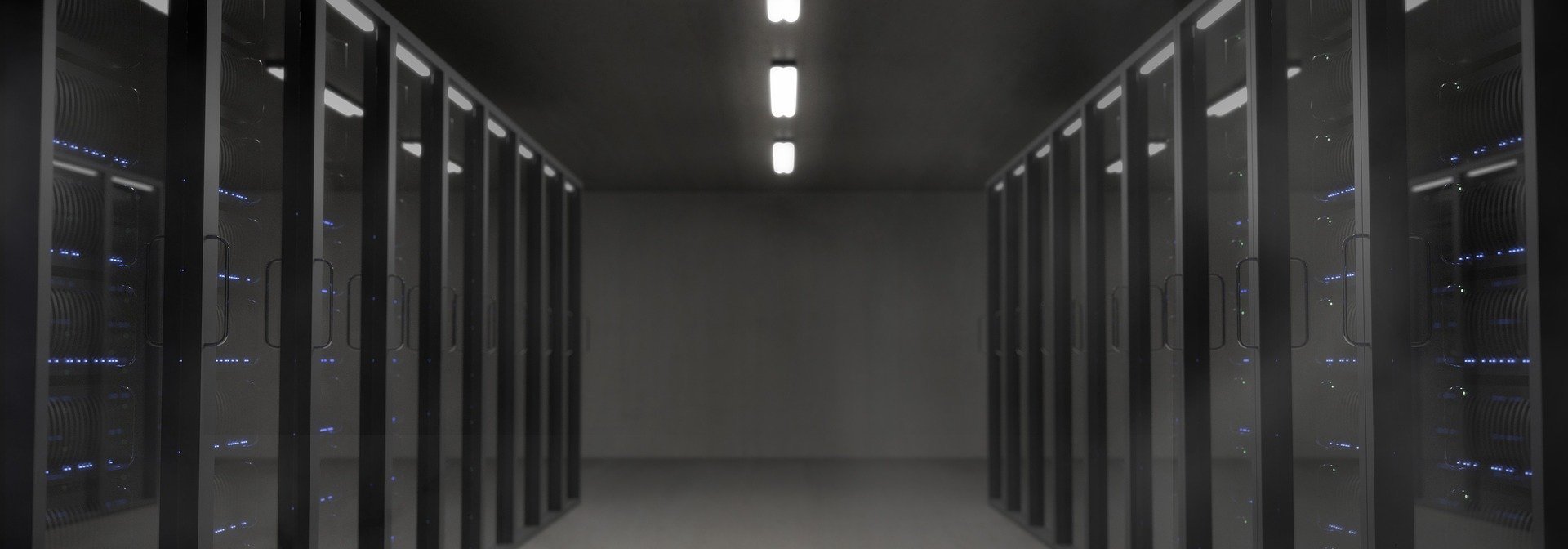
Digital Steel Innovation Hub
Task 4 Team
-
Prof. Cinzia Giannetti
Swansea University
-
Prof. Arnold Beckmann
Swansea University
-
Connor Blake-Hurley
Swansea University
-
Dr Kayla Lakshmanan
Swnsa University (MMSC)
-
Dr Robert Gibbs
Swansea University (MMSC)
-
David Ireland
University of Warwick
Introduction
The steel industry produces more than 1.7bn tonnes of steel per year and accounts for approximately 10% of global carbon emissions. Industrial Digital Technologies, such as wireless sensors, and advanced analytics offer tremendous opportunities to reduce the environmental impact of steel making by improving energy and resource efficiency and reduce scrap rate. Despite the availability of large volume of data, the steel industry is lagging in the exploitation of their data assets. Steel plants are large scale and complex; they have been operating for a long-time utilising legacy equipment alongside newer machineries, hence are often challenged by poor data quality. In addition, they rely heavily on the knowledge of expert operators and metallurgist to achieve optimal process operations.
Task 4 (Digital Steel Innovation Hub) is working with industrial partners in the steel industry and its supply chain to develop data driven innovations which will improve energy and material efficiency of steel making. Task 4 will develop new knowledge, tools, and applications of novel sensor technologies, fused with physics informed AI models and knowledge modelling to create actionable insight during manufacture. It will develop new approaches to enable safe and secure materials data sharing and integration throughout lifecycle.
Outcomes
The initial aim has been to create a data-driven step-change improvement in the competitiveness of UK end-to-end steel supply chains. It has aimed to utilise recent developments in technology to both harness and analyse data that can bring to improve the value-add and productivity of products, processes, and supply chains in the UK steel industry. Since then, the focus shifted towards exploring the use of semantic technologies to address the challenges related to the steel supply chains. Developed originally in the context of the semantic web, the aim is to give meaning to all kind of digital information, with the aim to make that information understandable for machines to enable advanced information processing and reasoning. In addition, semantic technologies have been very successful in digitising human knowledge in form of expert systems, and have successfully been used to reason about knowledge, data and processes in industrial domains.
Following the award of further funding, (Made Smarter Innovation: Materials Made Smarter Research Centre) the scope of Task 4 and 5 work has been extended. Specifically, the extended research team is now developing and validating new AI physics informed methods derived from coupling sensor-based information with physical simulations applied to the Hot Mill and Blast Furnace processes. Furthermore, research is currently being undertaken towards the development of common definitions, representations and metadata approaches to allow materials data sharing and integration throughout lifecycle. This activity involves organising workshops with industry stakeholders and researchers in material, data science, circular economy, and social sciences to gather requirements and co-develop a data-sharing platform that will form the basis of a standardised ‘material passport’.
The research team is exploring different aspects of data-driven innovations, including data sharing and integration and the development of novel predictive analytics to derive insights into process operation and guide optimisation of steel making processes.
The key deliverables to date are listed below:
We have developed a Common Reference Ontology for Steelmaking (CROS), which serves as a shared steelmaking resource and capability model that aims to facilitate knowledge modelling, knowledge sharing and information management . The functionality and usefulness of CROS has been evaluated and tested on a condition-based monitoring and maintenance task for cold rolling mills at Tata Steel UK.
Research has been proposed to develop Stream Reasoning for real-time predictive maintenance, building on the domain ontology CROS as a static knowledge model. The Stream Reasoner enables continuously query and reasoning on real-time data.
We have tested ideas around hybrid AI that combine knowledge technologies with statistical AI methods like Machine Learning, with the aim to integrate human knowledge with statistical AI for improved reasoning and decision capabilities.
We have developed and evaluated novel predictive analytics methodologies using large scale heterogeneous datasets collected from steel plants, including: i) prediction of [Si] in Blast Furnace; ii) Machine Learning enabled automated root cause analysis of width defects in Hot Mill processes; iii) estimating the remaining useful life of rolls in cold rolling mill; iv) remoting monitoring of steel processes using computer vision.
We have identified key implementation choices for blockchain technology that significantly impact the decisions involved in material passport creation.
The research has application to industry as it will produce proof of concepts and demonstrators of data and knowledge driven approaches to improve capabilities and efficiencies in the steel industry. This will require close collaboration with industrial partners and demonstration of use cases. The research will produce tangible impacts in terms of improvement of manufacturing processes, contributing to the wider goal of decarbonisation of the steel sector. The main barriers to implementation in industry are the lack of skills and capabilities in data driven innovations, lack of trust and issues with availability of good quality data.
Next Steps
Hybrid Modelling
Next stages will evaluate novel hybrid approaches that will enhance current modelling and data analytics capabilities, allowing to exploit the hidden potential of existing data assets to drive productivity improvements and sustainability. The aim is to provide a set of ontologies (developed in Task 20), data integration methods and guidelines that will enable integrate humans’ decision making and the vast tacit knowledge within existing modelling and analytics frameworks. In this way we will contribute to enhance our understanding of the application of hybrid methods in manufacturing, which is a relatively unexplored field. We believe that these hybrid technologies will support the realisation of high-fidelity digital twin models by integrating human and computer-generated knowledge into predictive platforms, ultimately leading to improved decision-making capabilities and optimal operations.
Blockchain
We are exploring some of the key implementation choices for blockchain technology, evaluating cost implementations and security (including layer 1, layer 2, side chains, and public and private blockchains). The next step will be to advance blockchain applications for material passports with examples based inside the steel supply chain to aid sustainability and circularity work.
Figure 1: Schematic depiction of the Digital Steel Innovation Hub (DSIH) within SUSTAIN